New perk! Get after it with local recommendations just for you. Discover nearby events, routes out your door, and hidden gems when you sign up for the Local Running Drop.
A step-by-step look at how Tyr’s triathlon wetsuits are made.
Written by: Aaron Hersh
Step 1: Shape the suit
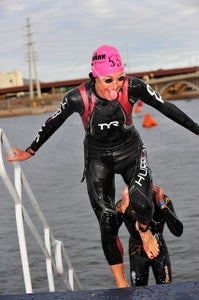
Tyr started the design process with a focus group of triathletes that told the designers how they want the suit to feel in the water and how it should alter their stroke. They strove to design anatomically correct panels that follow contours of typical male and female physiques to minimize restriction, and they used a mannequin with malleable dimensions to ensure the panels wrap smoothly around a swimmer’s body without placing seams over the important moveable segments. All three Tyr suits use the same panel patterns to ensure proper fit at every level.
Step 2: Decide on the panel characteristics
The three major characteristics of each individual wetsuit panel are insulation, buoyancy and stretch. According to Tyr’s wetsuit designers, “A thinner suit will stretch more in key areas (such as the shoulders) but might not be buoyant enough to lift the legs of a lower level swimmer,” so Tyr matches the materials used in its suits to meet the needs of different types of swimmer. Its high-end suits, aimed at experienced swimmers, are designed primarily for flexibility in the upper body and buoyancy in the lower body. To achieve these characteristics, Tyr builds the upper body of their flagship suit, the Category 1, with 1.5mm thick neoprene panels. Its entry-level suit, the Category 5, uses thicker material throughout the torso, which is both more buoyant and less flexible than the Category 1.
Step 3: Make the neoprene
Wetsuit neoprene begins as polychoroprene powder. The Yamamoto Corporation, which makes Tyr’s neoprene, adds a proprietary mix of ingredients to the powder in order to fine-tune the material’s elasticity, color, buoyancy and several other properties. This mixture is made into a doughy substance and, with the help of pressure and heat, squished into sheets of neoprene. Yamamoto applies a coating to the neoprene used for the Category 3 and Category 5 suits to reduce the friction between the suit and the water.
Step 4: Assemble the suit
Tyr assembles the neoprene panels using both glue and thread to ensure a connection that is both strong and watertight. They use a proprietary bonding process to attach its compression panels, and Tyr is tight-lipped about this method. The cloth inner liner is glued onto the neoprene and sewn in place with flatlock stitching that reliably holds the suit together without compromising flexibility.
Step 5: Testing
Instead of quantitatively measuring a suit’s speed, Tyr designed the Hurricane suits with the philosophy that a comfortable suit is a fast suit, and it relied heavily on its sponsored athletes to refine the designs. Andy Potts swam in early versions of the Hurricane wetsuits and provided feedback about how to tweak the suit to maximize comfort and the swim experience. When he first swam in a prototype suit with Tyr’s free-moving back panel he gave his seal of approval by telling the designers, “You guys finally figured it out.” They stuck with the design.